Asynchronous, standard and brake motors – 120Hz
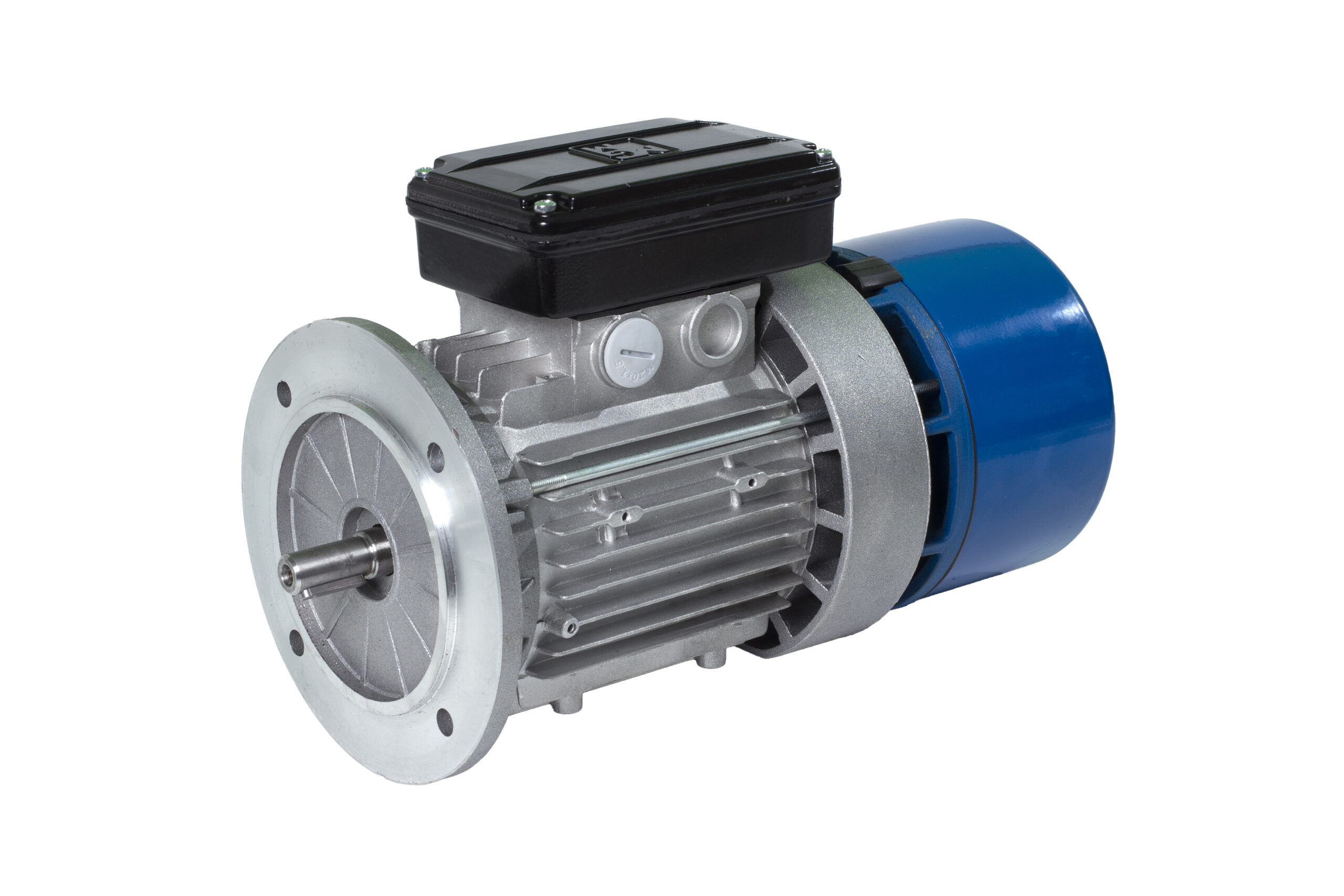
The “R” Series is made up of a new generation of asynchronous standard motors (SMR) or brake motors (BAR or BMR), 4 and 6 poles and IEC frame sizes from 56 up to 132.
Available nominal torques range is from 0.4Nm to 37Nm on 4 pole motors while it’s from 3.88Nm to 54.71Nm on 6 pole motors. R series motor is designed to be controlled by inverter only. The reference frequency at a voltage of 400V is 120Hz instead of 400V 50Hz.
The special technology allows to the R series motors to have the following features:
- constant torque from 3 to 120Hz
- torque close to the nominal one at 0 rpm (only in a closed loop vector system)
- higher Power Density (same power in smaller motor sizes)
- reduced moment of inertia compared to a motor with same power (high dynamics)
- faster acceleration and deceleration times
- excellent behaviour during transients (4 poles) and in continuous duty (6 poles)
- optimized for use with different types of inverters in the market
- balancing suited for operation with high acceleration
- standard motor sizes and mounting
- low noise
- standard electrical wiring
- encoder option available
- user friendly product (connectors not needed)
On standard, R series motors are equipped with thermal protectors, rotor and stator magnetic steel with advanced magnetic properties, motor winding specifically designed and impregnated for operation at high frequency, higher grade rotor balancing and bearings resistant to high rotation speed.
All the options of standard motors series are also available for the R Series IP54 enclosure rating is factory standard for brake motors while IP55 for standard motors. Enclosure rating up to IP56 is available on request. All motors can be provided either with an encoder or encoder ready.
The sectors where they are most used are in automation, packaging, ceramics, conveyor belts, automatic warehouses, etc… The typical applications are primarily concentrated on machines that use both asynchronous motors driven by inverters and brushless ones, especially in intermittent duty.
In the first case (replacement of asynchronous motors), they are indicated in all those applications in which the increase in speed leads to an operation at a frequency that is higher than the basic frequency of the motor with a subsequent decrease in torque. Specifically, the application of these motors allows to keep the gear box reduction ratio unchanged while increasing the frequency without problems.
Motors in the “R” series offer more adjustment possibilities (wider frequency range), better dynamic characteristics, similar or less energy consumption with smaller motor size and weight at equal power.
Using this product instead of an asynchronous motor makes an increase in transmission ratio necessary if you wish to decrease the size of the motor at equal power.
The reduction in size and weight at same power is very evident: this translates into a savings for the customer about the cost of the power transmission (as motor unit + gearbox) and the cost of the machine structure.
Using these motors makes also possible to rise the lower motor frequency, moving to a speed range that doesn’t need a forced cooling system (an appropriate reduction ratio must be chosen).
To maximize the advantages, we recommend using a reduction gear unit rather than a worm gearbox.
Replacing brushless motors: these are a valid alternative to servo motors in all applications in which a very strong dynamic is not required and in which a strict interpolation between the two motors is not needed. Compared to a brushless motor, the advantages are a reduction in cost, the absence of dedicated cables and connectors, a reduced maintenance and an extremely simple use that does not require specialized staff.
Definitively this new product allows:
- to think in a new way the process regarding the machine motorization
- to use an asynchronous motor instead of a brushless one
- to have smaller and lighter machines than current ones with equal power
- to have greater speed adjustment intervals
- to have an increased efficiency
- to have a reduced inertia at equal power
- to have a product that is simpler to use
- to have the same accessories as the standard product (encoder, power ventilation, etc.)
- to use any type of commercial inverter in the market
- to eliminate forced ventilation in many cases
- many industrial sectors have standardized certain types and brands of inverters. “R” series motors were designed and optimized to be extremely versatile and able to maintain the same performance with all major commercial drives This feature means not changing its standard and being able to use the most suitable inverter